Material Selection Advantages: Automotive rivet nuts are typically made from lightweight materials such as aluminum alloy or titanium alloy, offering a higher strength-to-weight ratio compared to traditional steel bolts and nuts. This material selection not only reduces the weight of individual components but also meets the requirements for strength and durability, particularly in terms of structural strength and fatigue resistance, which are often challenged in automotive engineering.
Design Optimization: Rivet nuts allow engineers greater flexibility in optimizing structures during the design process. Due to their compact and high-strength properties, the number and complexity of components can be reduced, leading to a lower overall weight. For instance, in body structures, the use of rivet nuts enables the integration of more fastening points, eliminating unnecessary structural supports, thereby reducing body weight and enhancing the vehicle's dynamic performance and fuel efficiency.
Improved Energy Efficiency: A vehicle's overall weight directly impacts its energy efficiency, including fuel consumption and emissions. By lightening the weight of vehicles, rivet nuts help reduce the load on the powertrain, minimize power losses, and require less energy to accelerate and maintain cruising speeds. These factors are crucial for meeting the modern automotive industry's demands for environmental friendliness and fuel economy.
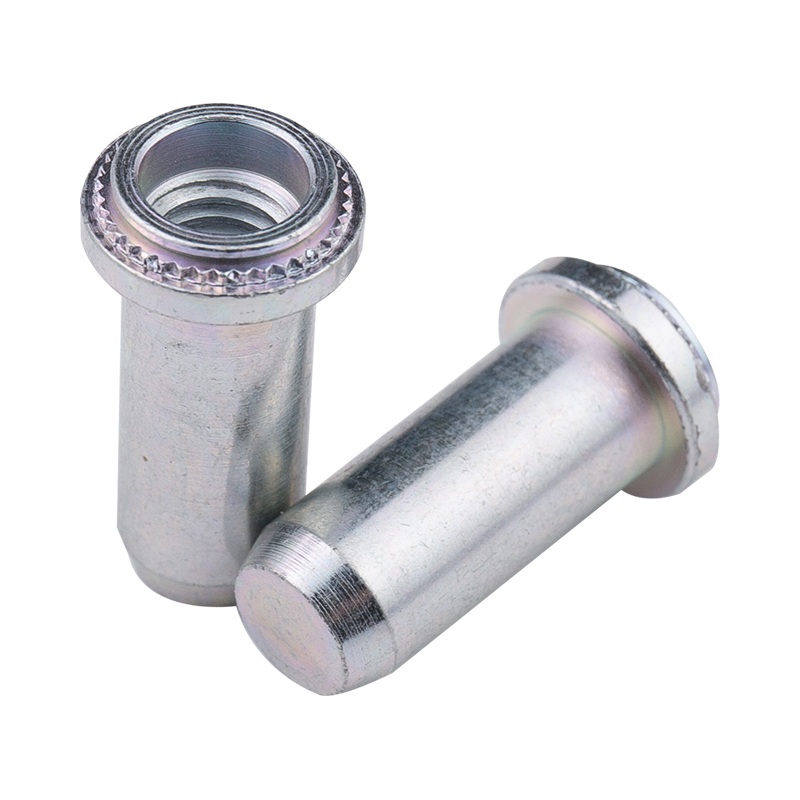
Manufacturing Cost and Efficiency: While the initial cost of rivet nuts may be higher, they can lower overall manufacturing costs by simplifying the assembly process and reducing the number of required components. In the overall vehicle lifecycle cost consideration, the use of Rivet Nuts can lead to long-term economic and environmental benefits.
Vibration and Noise Control: Rivet nuts can provide more secure connections, reducing looseness and vibration between components, thereby lowering noise and vibration generated by the vehicle during operation. This not only improves ride comfort but also contributes to the overall quality perception of the vehicle.
Environmental Adaptability: The material selection and design characteristics of rivet nuts make them perform well in various environmental conditions, including high temperatures, humidity, and chemical corrosion. This allows for their widespread application in various parts of the vehicle, such as engine compartments and underbody components, ensuring long-term reliability and safety.
Quick Repair and Maintenance: Compared to traditional bolts and nuts, rivet nuts are often easier to install and remove quickly. This is particularly important for vehicle repair and maintenance work, significantly reducing downtime and improving efficiency and throughput at repair facilities.
Innovation and Technological Advancement: As technology advances, the design and manufacturing of rivet nuts are also constantly innovating. For example, some modern rivet nuts may incorporate smart sensor technology to monitor connection status and provide real-time data feedback, enhancing vehicle safety and reliability.