Galvanic corrosion is a common challenge in engineering and construction, particularly when dissimilar metals are used in contact with each other. This phenomenon occurs when two metals with different electrochemical potentials are immersed in an electrolyte, creating a galvanic cell that accelerates the corrosion of the more reactive metal. Copper bolts play a crucial role in preventing galvanic corrosion in mixed-metal assemblies, and understanding their mechanisms can enhance the longevity and reliability of these structures.
Noble Metal Properties
Copper is classified as a noble metal, which means it is less reactive than many other metals, such as aluminum or steel. When copper bolts are used in assemblies with these more reactive metals, they help to create a protective barrier that minimizes the likelihood of corrosion. The inherent properties of copper allow it to resist corrosion, thus protecting the integrity of the assembly.
Electrochemical Potential
In a galvanic couple, the difference in electrochemical potential between the two metals determines which one will corrode more rapidly. Copper has a higher electrochemical potential compared to many common metals. By using copper bolts, the corrosive reactions that typically affect the more reactive metal are significantly reduced, providing a longer-lasting solution for mixed-metal assemblies.
Minimizing Contact
The design of copper bolts can also play a role in reducing the surface area of contact between dissimilar metals. By minimizing contact points, the electrochemical reactions that lead to galvanic corrosion can be limited. Additionally, copper bolts can be paired with insulating materials or coatings to create a physical barrier, further preventing direct electrical contact and reducing the risk of corrosion.
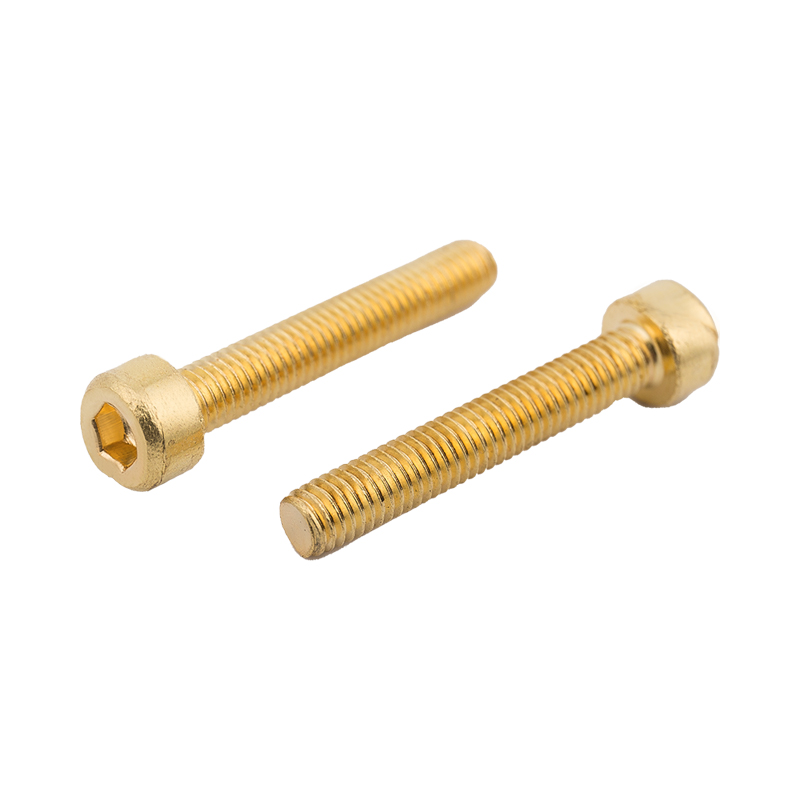
Sacrificial Action
In scenarios where copper bolts are fastening more reactive metals, the bolts can corrode preferentially. This sacrificial action protects the underlying metal from corrosion, extending the life of the entire assembly. Over time, this can significantly enhance the durability of structures exposed to harsh environments.
Natural Corrosion Resistance
Another advantage of copper is its natural resistance to corrosion. When exposed to the elements, copper forms a protective patina (copper oxide) on its surface. This layer not only shields the copper bolt itself but also offers some protection to adjacent metals, reducing overall corrosion rates.
Use of Sealants
Copper bolts can be effectively paired with compatible sealants or coatings that protect against moisture and electrolytes. These additional layers of protection further mitigate the risk of galvanic corrosion, ensuring that mixed-metal assemblies remain robust over time.
In summary, copper bolts are a valuable asset in preventing galvanic corrosion in mixed-metal assemblies. Their noble properties, higher electrochemical potential, and natural corrosion resistance contribute significantly to the longevity and reliability of structures. By understanding the mechanisms through which copper bolts mitigate corrosion risks, engineers and designers can make informed choices that enhance the durability of their projects.