Passivation is primarily a chemical process designed to enhance the corrosion resistance of stainless steel by cleaning the surface and promoting the formation of a protective chromium oxide layer. While passivation greatly improves the longevity and durability of stainless steel screws in corrosive environments, it has minimal direct impact on their mechanical strength and fatigue resistance. However, there are some indirect effects that contribute to maintaining and even improving the overall performance of stainless steel screws over time.
Corrosion Prevention and Mechanical Strength
Stainless steel screws are designed to endure mechanical loads, such as tension, shear, and compression, without deforming or breaking. The mechanical strength of the screw is determined by the material's internal structure, such as its alloy composition, heat treatment, and manufacturing process, not by passivation itself.
However, corrosion can weaken screws over time, leading to a reduction in mechanical strength. When a screw starts to corrode, tiny cracks or pits may form on its surface, acting as stress concentrators that reduce its load-bearing capacity. Corrosion can lead to localized areas of weakness that make the screw more susceptible to breakage under mechanical stress.
By removing surface contaminants and enhancing the formation of the chromium oxide layer, passivation effectively reduces the chances of corrosion forming on the screw. This helps preserve the screw's structural integrity over time, allowing it to maintain its original mechanical strength for longer periods.
Fatigue Resistance and Surface Integrity
Fatigue resistance refers to a material's ability to withstand repeated or cyclic loading without developing cracks or failing over time. Stainless steel screws used in dynamic environments—such as in machinery, vehicles, or bridges—often face fatigue stress.
Surface imperfections, such as microcracks or embedded foreign particles, can accelerate fatigue failure. These imperfections act as initiation points for cracks, which then propagate under cyclic loads. The passivation process helps by removing impurities like iron particles or machining residues from the surface of the stainless steel screws. This results in a smoother, cleaner surface with fewer stress concentrators, which can slow down the initiation of fatigue cracks.
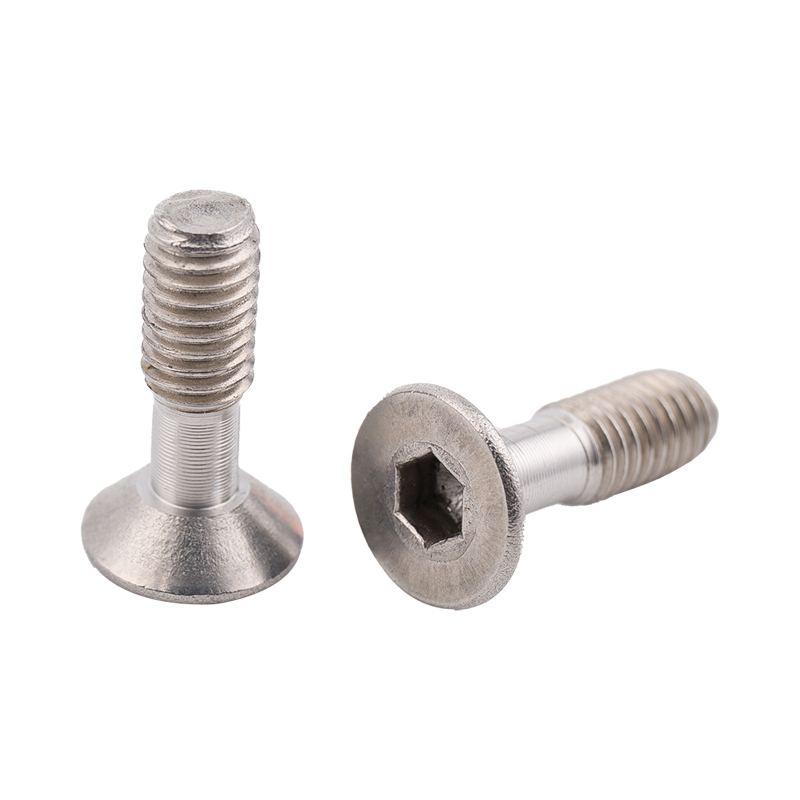
While passivation doesn't directly improve the inherent fatigue resistance of the material, it optimizes the surface condition of the screw, reducing the risk of surface-related failures. In environments where fatigue is a concern, this cleaner surface can make a meaningful difference in the screw's lifespan.
Indirect Influence: Reducing Surface Defects
During manufacturing, stainless steel screws can pick up surface contaminants or mechanical damage, such as scratches or tool marks, which might weaken the surface. If not removed, these defects can compromise the mechanical performance of the screw.
Passivation acts as a "final cleanup," removing contaminants and smoothing out minor imperfections. While this does not change the underlying strength of the metal, it does help the screw perform closer to its intended mechanical limits by minimizing surface defects that could otherwise compromise performance.
While passivation doesn't directly alter the mechanical strength or fatigue resistance of stainless steel screws, it plays a crucial role in maintaining and preserving these properties by preventing corrosion and improving surface quality. By removing contaminants and fostering a smooth, protective layer, passivation helps stainless steel screws resist degradation in harsh environments, ensuring they retain their strength and fatigue resistance over long periods of use.
In essence, passivation indirectly contributes to the long-term mechanical performance of stainless steel screws by protecting their surface integrity, which in turn preserves their strength and fatigue resistance against environmental factors and cyclic stresses.