The manufacturing process of stainless steel nuts, including casting, forging, and machining, has a significant impact on their mechanical properties, strength, durability, and overall quality. Each method offers unique advantages and considerations, affecting the final performance of the nuts in different applications. Here's how these processes influence the quality and properties of stainless steel nuts:
1. Casting
Casting involves pouring molten stainless steel into a mold to create the nut shape. The metal is then cooled and solidified, and the nut is removed from the mold.
Mechanical Properties:
Porosity: Casting can introduce small voids or pores in the material, which may reduce the strength and fatigue resistance of the nut. This can be problematic in high-stress applications where integrity is critical.
Tensile Strength: Cast nuts typically have lower tensile strength compared to forged or machined nuts because the cooling rate and solidification process can lead to a more uneven grain structure. This can make them more susceptible to cracking or deformation under load.
Surface Finish: Cast nuts may have a rougher surface finish compared to nuts made by other methods. Additional finishing processes, such as grinding or polishing, may be required to improve the surface quality.
Advantages:
Cost-Effective: Casting is generally more affordable for producing large volumes of nuts with complex shapes or intricate designs, especially in industries like automotive or construction where cost is a key factor.
Versatility: Casting is suitable for creating large, intricate parts or nuts with complex geometries that would be difficult or uneconomical to achieve with forging or machining.
Applications:
Low to medium stress applications where cost is a primary concern, such as in construction or non-critical machinery parts.
2. Forging
Forging involves applying heat and pressure to stainless steel to shape the nut. The metal is heated to a high temperature and then compressed in a die to form the desired shape.
Mechanical Properties:
Grain Structure: Forging aligns the metal’s grain structure, which improves the nut’s strength, toughness, and resilience. The process refines the grain, making it more uniform and oriented in the direction of the applied stress. This results in better mechanical properties, especially in terms of fatigue resistance.
Tensile Strength: Forged stainless steel nuts tend to have higher tensile strength and impact resistance than cast or machined nuts, making them ideal for high-stress applications.
Ductility: Forging also improves the ductility of the material, which makes the nuts less prone to cracking or breaking under tension.
Advantages:
High Strength: Forged nuts are typically much stronger than cast nuts, especially in critical applications that require high load-bearing capacity or durability.
Uniformity: The process provides a more uniform material structure, with fewer imperfections or weaknesses, making forged nuts ideal for safety-critical applications.
Less Material Waste: Forging is generally more material-efficient, as it uses solid metal rather than molten metal, reducing waste during production.
Applications:
High-stress applications, such as in aerospace, automotive, and oil and gas industries, where durability and strength are paramount.
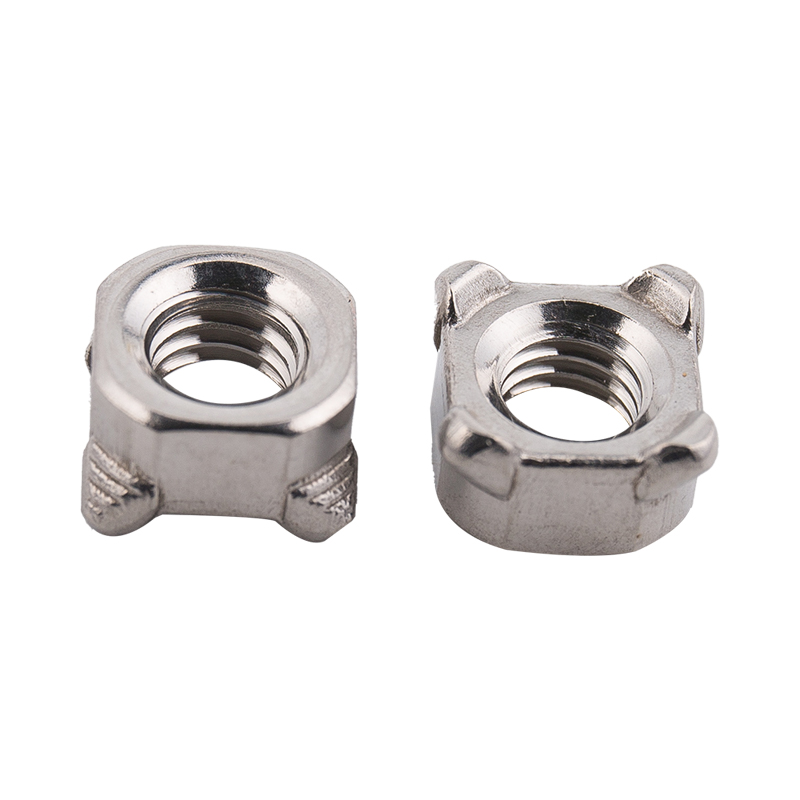
3. Machining
Machining involves cutting or shaping a piece of stainless steel using tools like lathes, mills, or drills. For nuts, this often means starting with a bar or billet of stainless steel and removing material to achieve the desired shape and size.
Mechanical Properties:
Precision: Machining allows for very precise control over the dimensions and surface finish of the nut. This is critical in applications where tight tolerances are required, such as in electrical equipment or medical devices.
Surface Finish: Machining typically results in a smoother surface finish than casting or forging, reducing friction and wear when the nut is used in applications that involve moving parts or mechanical connections.
Strength: While machining can provide excellent precision and surface quality, the mechanical properties of the nut are primarily dependent on the initial material quality (i.e., the billet used for machining). If the material is not heat-treated or forged before machining, the strength might be lower compared to a forged nut.
Advantages:
High Precision: Machining is ideal for producing nuts with tight tolerances or custom designs. It allows manufacturers to create nuts with complex features or fine threads that might be difficult to achieve through casting or forging.
Customization: Machining provides flexibility for creating small batches or specialized parts, especially when customized nut sizes or shapes are needed for unique applications.
Surface Finish: It provides an excellent surface finish with minimal need for additional finishing processes.
Applications:
High-precision industries, such as aerospace, medical devices, and electronics, where accuracy, surface finish, and customization are important.
4. Heat Treatment and Finishing
Regardless of whether the nut is cast, forged, or machined, heat treatment and surface finishing are often used to further enhance its mechanical properties and quality.
Heat Treatment:
Hardening or tempering processes can be applied to increase the nut’s strength and resistance to wear. Stainless steel nuts may undergo processes like quenching, annealing, or carburizing to achieve the desired balance of hardness and ductility.
Finishing:
Polishing, plating, or passivation can be used to improve the appearance, corrosion resistance, or smoothness of the surface, which is particularly important in industries like food processing and medical where hygiene and appearance are crucial.
Impact on Overall Quality
Durability: Nuts made by forging or machining typically have higher durability and resistance to fatigue and wear, which are essential in high-performance applications.
Cost vs. Performance: The choice of manufacturing method affects the cost of production. Forged nuts are more expensive due to the energy and time required, but they offer higher strength and reliability. Cast nuts, while less expensive, may not offer the same mechanical properties.
Precision and Tolerances: Machining excels in high-precision applications where nuts need to fit exact specifications. This method is ideal when dimensions or threading need to be precise and uniform.