The service life of a shaft core is influenced by a variety of factors that relate to its design, materials, manufacturing process, operational environment, and maintenance practices. Here are some key factors:
Material Properties
Material Quality:
The type of material used (e.g., steel, aluminum, composite materials) significantly impacts the durability and wear resistance of the shaft core.
Hardness and Toughness:
The balance between hardness and toughness affects the shaft core’s ability to resist wear and absorb impact without cracking.
Design Considerations
Geometry and Dimensions:
The design, including the diameter, length, and cross-sectional shape, affects the stress distribution and load-carrying capacity.
Surface Finish:
A smoother surface finish can reduce friction and wear, prolonging the service life.
Load Distribution:
Evenly distributed loads reduce localized stress concentrations that can lead to premature failure.
Manufacturing Process
Quality Control:
Consistent quality control during manufacturing ensures that defects such as cracks, voids, or inclusions are minimized.
Heat Treatment:
Proper heat treatment processes, such as annealing, quenching, and tempering, enhance the material properties and improve fatigue resistance.
Operational Environment
Load Conditions:
The type, magnitude, and frequency of loads (static, dynamic, cyclic) directly affect fatigue life and wear.
Operating Temperature:
High temperatures can affect material properties, leading to thermal fatigue and degradation.
Corrosive Environment:
Exposure to corrosive substances (e.g., chemicals, saltwater) can lead to corrosion and material degradation.
Contaminants:
Presence of dust, dirt, or other contaminants can increase abrasion and wear.
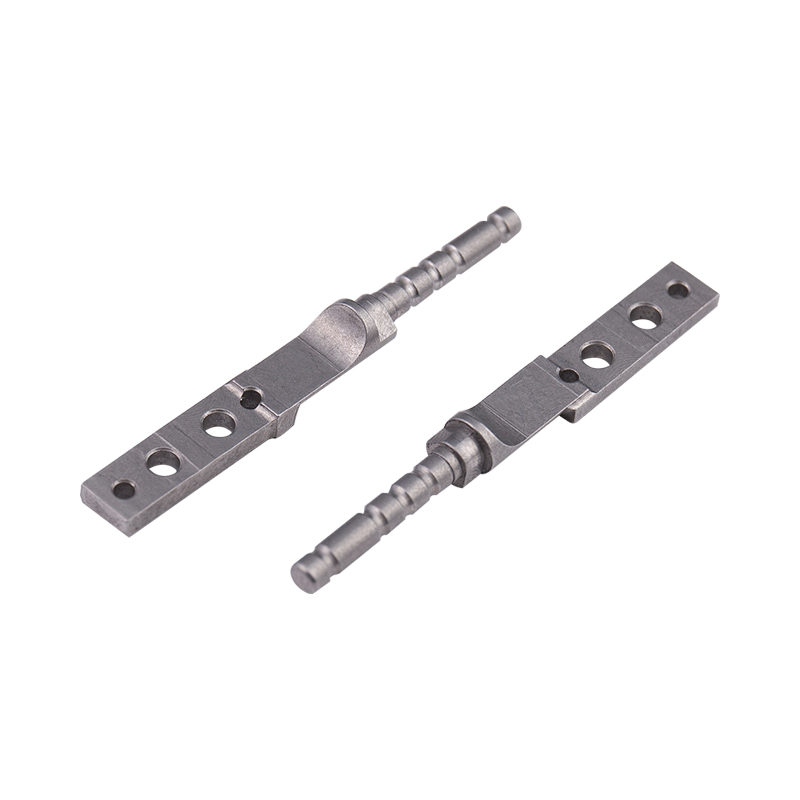
Maintenance and Usage
Lubrication:
Proper and regular lubrication reduces friction and wear, preventing overheating and material degradation.
Alignment and Balancing:
Proper alignment and balancing of the shaft reduce undue stress and vibration, which can lead to premature failure.
Regular Inspections:
Routine inspections can identify wear, misalignment, or other issues before they lead to failure.
Mechanical and Thermal Stresses
Fatigue Loading:
Repeated cyclic loading can cause fatigue failure over time. Designing for appropriate fatigue life is crucial.
Thermal Expansion:
Differential thermal expansion can induce stresses, especially if the shaft is subjected to fluctuating temperatures.
Surface Treatments and Coatings
Protective Coatings:
Applying coatings such as plating, anodizing, or specialized wear-resistant coatings can protect the shaft core from corrosion and wear.
Surface Hardening:
Techniques like carburizing, nitriding, or induction hardening can increase surface hardness and wear resistance.
External Factors
Shock and Impact Loads:
Sudden shocks or impacts can cause immediate or cumulative damage, affecting the shaft’s longevity.
Vibration:
Continuous vibration can lead to fatigue and fretting wear, reducing the shaft’s service life.
By considering these factors during the design, manufacturing, and operational phases, the service life of a shaft core can be significantly extended, ensuring reliable performance and reducing the need for frequent replacements.