Effective fastening techniques for stainless steel screws involve a combination of proper installation methods, tools, and considerations for the material being fastened. Here are some of the most effective techniques:
Pre-drilling:
For hard materials, pre-drilling pilot holes can prevent splitting and ensure proper alignment. The pilot hole should be slightly smaller than the screw's diameter to allow for a tight fit.
Using the Right Tool:
Utilizing a high-quality screwdriver or drill with the appropriate bit is crucial. For stainless steel screws, using a drill with a slower speed can reduce the risk of overheating, which can lead to galling (friction-induced damage).
Torque Control:
Applying the correct amount of torque is essential. Over-tightening can strip the threads or damage the material, while under-tightening can lead to loosening. Using a torque wrench can help achieve the right tension.
Thread Lubrication:
Applying a lubricant (such as anti-seize compound) to the threads can reduce friction and prevent galling, especially in stainless steel applications where metal-to-metal contact occurs.
Proper Thread Engagement:
Ensuring full thread engagement with the mating material enhances load distribution and holding power. This often involves using screws with a length suitable for the thickness of the materials being joined.
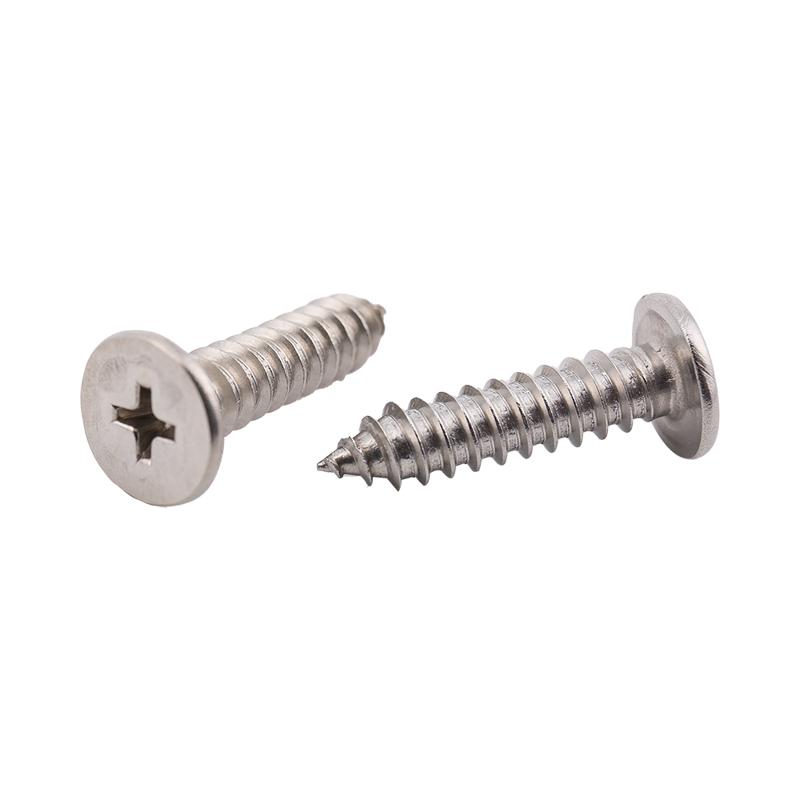
Using Washers:
In applications where load distribution is important, using washers can help spread the load and prevent damage to the surface being fastened. This is particularly useful in softer materials.
Vibration Resistance:
For applications exposed to vibrations, consider using locking mechanisms (like lock washers or nylon insert lock nuts) or thread-locking adhesives to prevent loosening.
Environmental Considerations:
In corrosive environments, using marine-grade stainless steel screws (like 316 grade) can enhance durability. Also, ensuring that dissimilar metals are isolated (using non-metallic washers) can prevent galvanic corrosion.
Correct Installation Technique:
When installing, start the screw slowly to ensure it engages properly. Once the screw is started, increase speed but remain cautious not to overtighten.
Regular Maintenance:
For applications subject to wear and tear, periodically checking and retightening screws can help maintain their integrity and performance.