Stainless steel bolts can be designed to meet the specific requirements of high-pressure or high-temperature applications through several key design and material considerations. Below are the factors that influence their performance in these demanding environments:
1. Material Selection
High-Temperature Resistance: Choose stainless steel grades with higher temperature resistance, such as Grade 316 or Grade 321, which contain higher levels of molybdenum or titanium for better resistance to heat and oxidation. These grades perform well in applications where temperatures exceed 500°F (260°C) and can withstand thermal expansion without losing strength.
Heat-Resistant Alloys: For extreme temperatures, special alloys such as Inconel or Hastelloy may be used, as they offer superior resistance to creep, oxidation, and thermal fatigue under high temperatures.
2. Thread Design and Geometry
Stress Distribution: To ensure the bolts can handle high-pressure environments, the thread design should focus on uniform stress distribution. Using fine threads (as opposed to coarse threads) can provide better tensile strength and resistance to stripping under high-pressure conditions.
Longer Threads or Threaded Inserts: For applications requiring high load-bearing capacity, longer threads or the use of threaded inserts can help distribute the pressure more evenly across the surface, reducing the risk of failure.
3. Bolt Size and Strength
Tensile Strength: Stainless steel bolts should be chosen with sufficient tensile strength to handle both axial and shear forces present under high pressure. Higher-strength stainless steels, such as Grade 17-4 PH, may be necessary for applications where the bolts are subject to higher loads or pressure.
Diameter and Length: The diameter and length of the bolts should be selected to handle the applied forces. For high-pressure applications, larger diameters can provide more surface area to better distribute pressure and prevent failure. The length must be sufficient to ensure that the bolt will hold components securely under the applied pressure.
4. Heat Treatment
Annealing or Solution Heat Treatment: Stainless steel bolts used in high-temperature environments should be annealed or solution heat-treated to relieve internal stresses and improve their ductility and corrosion resistance. Heat treatment also enhances the bolt's ability to resist creep deformation and maintain its shape under prolonged high temperatures.
Preloading: Ensuring the bolt is properly preloaded during installation will help maintain its integrity under high-pressure conditions. Controlled torqueing or tensioning ensures the bolt remains under a continuous force, preventing loosening and leakage in high-pressure systems.
5. Surface Treatments
Coatings: High-pressure and high-temperature environments often expose bolts to extreme wear and corrosion. Coatings such as ceramic or PTFE (polytetrafluoroethylene) can improve resistance to thermal cycling and oxidation. These coatings help reduce friction and wear while providing additional corrosion resistance.
Passivation: The bolts can undergo a passivation process to enhance the corrosion resistance of stainless steel, especially in environments exposed to acidic or chloride-rich conditions. Passivating the bolt ensures that the oxide layer on the surface is free of contaminants, reducing the risk of stress corrosion cracking under high pressure.
6. Bolting System and Fastening
Bolting Arrangement: In high-pressure applications, bolts may be used in multiple-bolt arrangements (such as flanged connections). The design should ensure even loading across the entire set of bolts to prevent localized stresses. Multiple fasteners are often needed to distribute pressure evenly and reduce the risk of failure in any one bolt.
Locking Mechanisms: High-pressure environments often require locknuts, locking washers, or thread-locking adhesives to prevent the bolts from loosening over time due to vibration or thermal cycling.
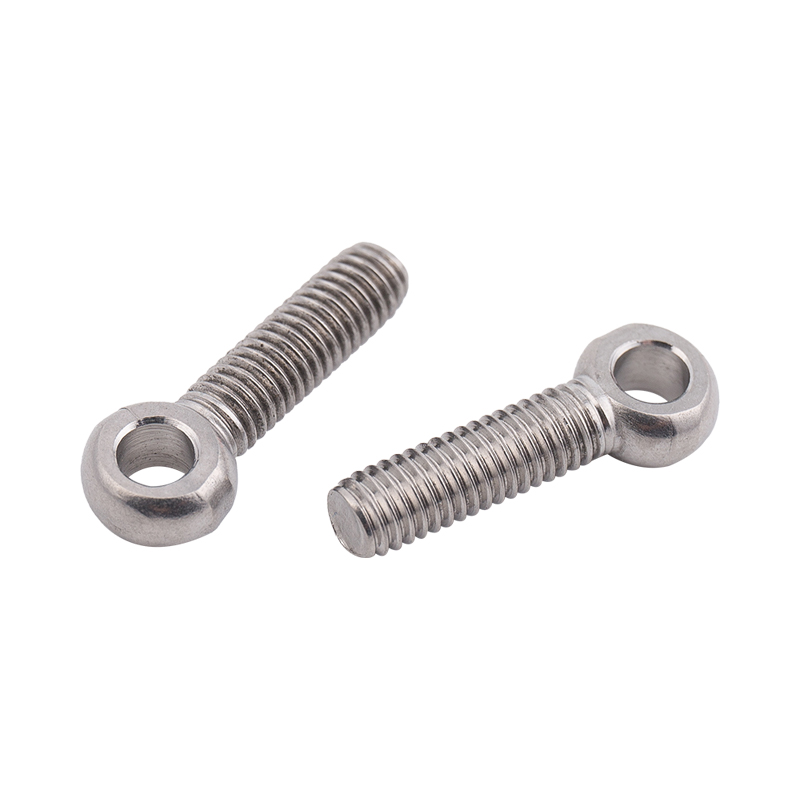
7. Stress and Fatigue Resistance
Fatigue Resistance: Stainless steel bolts in high-temperature or high-pressure environments are often exposed to cyclic loading, which can lead to fatigue failure. Selecting bolts with enhanced fatigue resistance (such as higher-strength alloys) or increasing the diameter and thread depth can help mitigate the risk of fatigue cracking.
High Pressure and Temperature Creep: Creep refers to the slow deformation of a material under constant stress over time. Bolts in high-pressure, high-temperature environments must be designed with materials that exhibit low creep rates, such as heat-treated stainless steel or specialized alloys.
8. Quality Control and Testing
High-Pressure Testing: To ensure the bolts meet the required standards, they should undergo hydraulic or pneumatic testing at pressure levels that replicate operational conditions. These tests confirm that the bolts can withstand leak-proof sealing and maintain structural integrity under real-world pressure.
Material Testing: Stainless steel bolts should be subjected to tests like tensile strength testing, hardness testing, and impact testing to verify that they can perform under both high-pressure and high-temperature conditions.