The presence of inclusions or microscopic defects in stainless steel bolts can significantly affect their fatigue resistance and overall strength in the following ways:
1. Stress Concentration
Inclusions, such as non-metallic particles (oxides, sulfides, or silicates) or microscopic defects (pores, cracks, or voids), act as stress concentrators. These imperfections disrupt the uniform flow of stress across the surface of the bolt, concentrating the applied forces around the inclusion or defect. This localized stress increase can lead to:
Initiation of cracks: Stress concentrations can initiate cracks, especially under cyclic loading or fluctuating stresses.
Premature fatigue failure: Cracks that start at inclusions or defects are often the starting points for fatigue failure, leading to crack propagation and eventual breakage of the bolt under lower stress levels than would be expected for a defect-free bolt.
2. Decreased Fatigue Strength
Stainless steel bolts are typically designed to withstand repeated loading and unloading, as seen in high-vibration applications (e.g., automotive, aerospace). However, inclusions or microscopic defects weaken the material, reducing its fatigue strength. This results in:
Lower fatigue life: Even minor imperfections can drastically reduce the number of load cycles the bolt can endure before failure.
Early onset of fatigue cracking: Small defects serve as starting points for cracks, which propagate more rapidly under cyclic loading, leading to earlier failure than bolts without such defects.
3. Reduced Tensile Strength
Inclusions and defects can also affect the overall tensile strength of stainless steel bolts, which is crucial for applications where high axial forces are involved. The effect on tensile strength can manifest as:
Localized weakening: Inclusions or microscopic defects reduce the material's ability to handle the tensile load evenly, causing it to fail at lower stress levels than expected.
Ductility loss: Some inclusions, particularly those with brittle characteristics, reduce the ductility of stainless steel. This makes the material less able to deform plastically before failure, increasing the likelihood of brittle fracture under high loads.
4. Impact on Structural Integrity
In high-stress environments, such as in pressure vessels or turbine engines, the structural integrity of stainless steel bolts is paramount. The presence of microscopic defects or inclusions:
Reduces fatigue life: This can be particularly critical in safety-critical applications where long-term durability is required.
Increases the risk of failure under dynamic loading: In applications with fluctuating or shock loads, these defects can dramatically increase the likelihood of failure, as the material's ability to withstand variable stress is compromised.
5. Creep and Corrosion Resistance
In some cases, inclusions can negatively affect the creep resistance (resistance to deformation under constant stress at high temperatures) and corrosion resistance of stainless steel bolts. This can further compromise their performance in demanding environments such as:
Elevated temperature applications: Defects or inclusions can lead to localized heating and accelerated oxidation, reducing the material's overall strength.
Corrosion initiation: Inclusions can create sites for corrosion to begin, especially in chloride-rich environments, leading to stress corrosion cracking (SCC) that worsens material degradation.
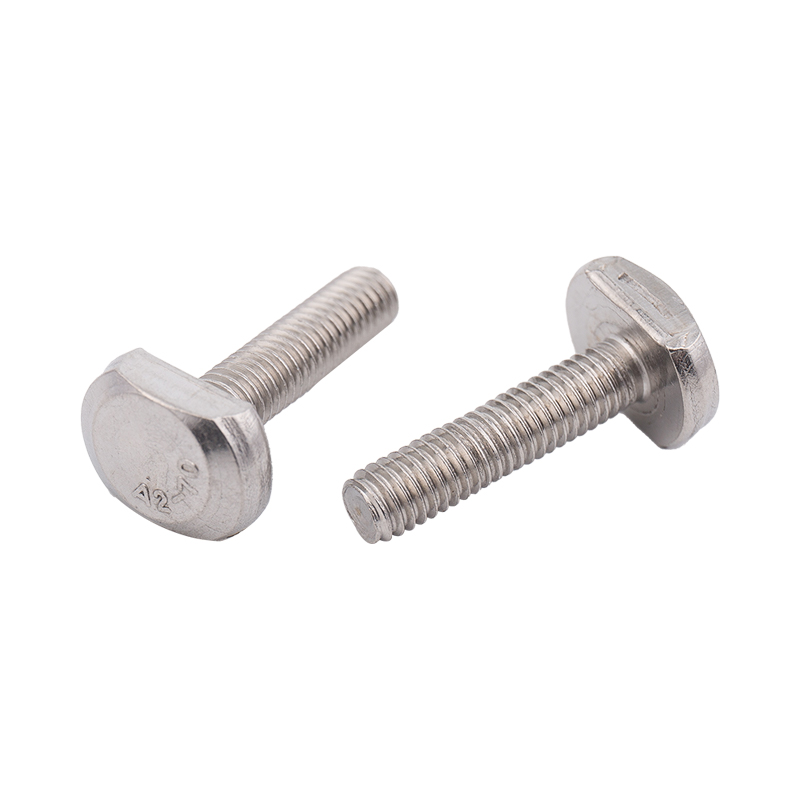
6. Testing and Quality Control
To mitigate these effects, stainless steel bolts undergo rigorous inspection and testing (e.g., using ultrasonic testing, X-ray inspection, or eddy current testing) to detect and eliminate any harmful inclusions or defects. Bolts are often subject to:
Tensile tests: To evaluate their load-bearing capacity.
Fatigue tests: To determine the number of cycles they can withstand before failure.
Non-destructive testing (NDT): To identify internal defects that could affect the strength and fatigue resistance of the bolts.