Stainless steel nuts play a vital role in the structural integrity of machinery and equipment across a variety of high-performance industries. From aerospace and automotive manufacturing to heavy industrial machinery and medical devices, the fasteners used in these applications must meet stringent performance criteria. But what is it about stainless steel nuts that make them so crucial in maintaining the safety, efficiency, and longevity of these critical systems?
One of the primary reasons stainless steel nuts are favored in high-performance industries is their superior mechanical properties. Stainless steel is renowned for its high tensile strength, which is essential when it comes to securing components that must withstand heavy loads, frequent vibrations, or constant mechanical stress. In automotive and aerospace applications, for example, fasteners must not only hold components together securely but also resist the forces generated by constant motion, pressure changes, and vibrations. Stainless steel nuts offer the strength required to ensure that parts remain intact under these extreme conditions.
In addition to tensile strength, stainless steel nuts also demonstrate excellent resistance to fatigue, a common issue in machines and engines subjected to continuous mechanical cycles. Fatigue failure occurs when materials crack or break due to repeated loading and unloading over time. Stainless steel, with its resistance to fatigue, ensures that nuts retain their strength even after thousands of cycles, thus minimizing the risk of fastener failure. This is particularly important in industries where safety is paramount, such as in the aerospace sector, where failure of a single fastener can result in catastrophic consequences.
Moreover, stainless steel nuts are highly resistant to extreme temperatures, making them ideal for use in environments where temperature fluctuations are common. Automotive engines, for example, operate at temperatures that can reach several hundred degrees Fahrenheit. Stainless steel nuts can withstand such temperatures without losing their strength or becoming brittle. This makes them suitable for critical engine parts, exhaust systems, and other components where both high temperatures and mechanical stress are present.
The durability of stainless steel nuts extends to their resistance to environmental factors such as humidity, UV radiation, and exposure to chemicals. In industries like petrochemical and pharmaceutical manufacturing, equipment is often exposed to corrosive substances and hazardous chemicals. Stainless steel nuts, due to their corrosion-resistant properties, help maintain the integrity of the machinery in these environments, ensuring that the fasteners do not degrade over time, which could lead to operational failures or unsafe conditions.
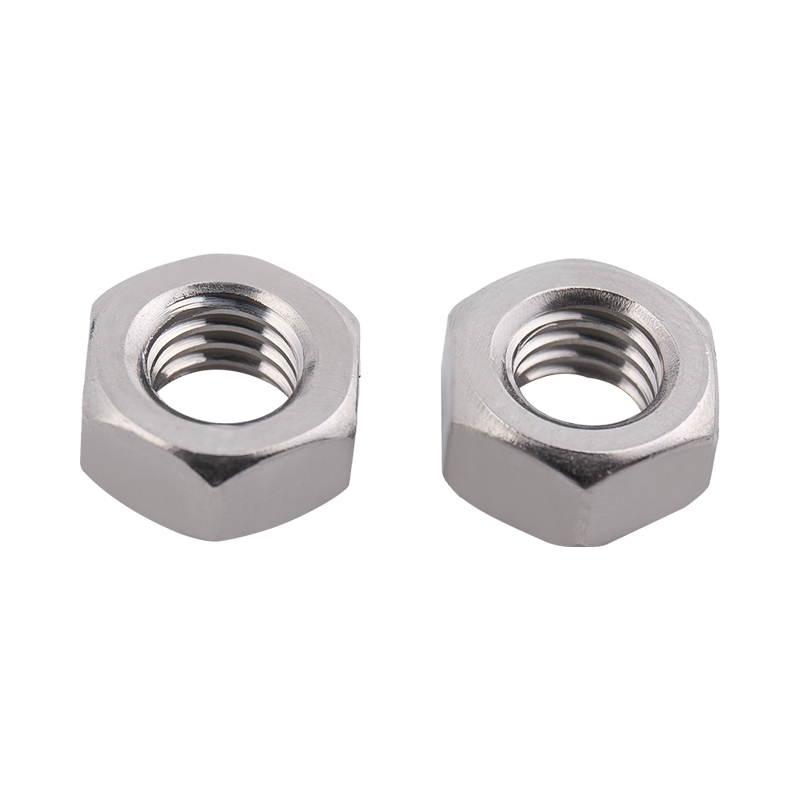
In the construction and infrastructure sectors, stainless steel nuts are indispensable in ensuring the structural integrity of bridges, buildings, and other large-scale projects. These fasteners are used to secure steel beams, joints, and other critical components, providing the strength needed to support the load-bearing requirements of these structures. Given their resistance to rust, corrosion, and wear, stainless steel nuts ensure that these vital components continue to function as designed over long periods, even in harsh weather conditions.
The use of stainless steel nuts also reduces the frequency of maintenance required for high-performance machinery. In industries where downtime is costly, the longevity and reliability of stainless steel fasteners help minimize the need for frequent repairs or replacements. This not only saves money but also improves the overall efficiency of operations.
While stainless steel nuts are essential for maintaining the structural integrity of critical machinery, it’s important to consider the specific type of stainless steel used in manufacturing the fasteners. The choice of grade, such as 304, 316, or 410 stainless steel, can impact the performance of the nuts in specific applications. For instance, grade 316 is often preferred for environments exposed to high levels of corrosive elements, while grade 304 is sufficient for general industrial applications.