Stainless steel nuts are widely regarded as indispensable components in a range of industries, particularly in high-stress environments where both mechanical performance and corrosion resistance are paramount. These fasteners are commonly used in the aerospace, automotive, and marine sectors, as well as in construction and heavy machinery. But what exactly are the factors that make stainless steel nuts the preferred choice in such challenging environments?
One of the most critical factors is stainless steel’s resistance to corrosion, particularly in environments where exposure to water, chemicals, and extreme temperatures is constant. Stainless steel is primarily composed of iron, chromium, and often nickel, with chromium being the key element that provides the material its corrosion-resistant properties. When chromium is exposed to oxygen, it forms a thin, passive oxide layer on the surface of the steel, preventing further oxidation and deterioration of the metal. This protective layer is highly effective, ensuring that stainless steel nuts retain their strength and durability even when subjected to moisture, salt, or acids.
In the marine industry, for example, stainless steel nuts are essential in preventing the rapid degradation of fasteners in saltwater environments. Saltwater is notorious for accelerating the rusting process in metals, yet stainless steel nuts, particularly those made from higher grades like 316 stainless steel, offer outstanding resistance to this type of corrosion. As a result, these fasteners are commonly used in ships, offshore rigs, and coastal infrastructure where long-lasting durability is crucial for safety and operational performance.
Similarly, in the automotive industry, stainless steel nuts are favored for their ability to withstand not only corrosive elements but also high temperatures. The engine components, exhaust systems, and other critical parts of vehicles are constantly exposed to extreme heat and environmental contaminants. Stainless steel’s ability to resist both heat and corrosion makes it an ideal choice for fasteners that must endure these harsh conditions for the vehicle’s entire lifespan.
Furthermore, stainless steel nuts exhibit impressive mechanical properties that contribute to their performance under high-stress conditions. They are capable of withstanding significant tensile loads and resisting fatigue over time, making them suitable for applications where heavy loads and constant vibrations are common. For instance, in industrial machinery or structural applications, the fasteners must not only resist corrosion but also ensure the integrity of the entire system. Stainless steel nuts provide reliable performance even under heavy mechanical stress, ensuring long-term stability.
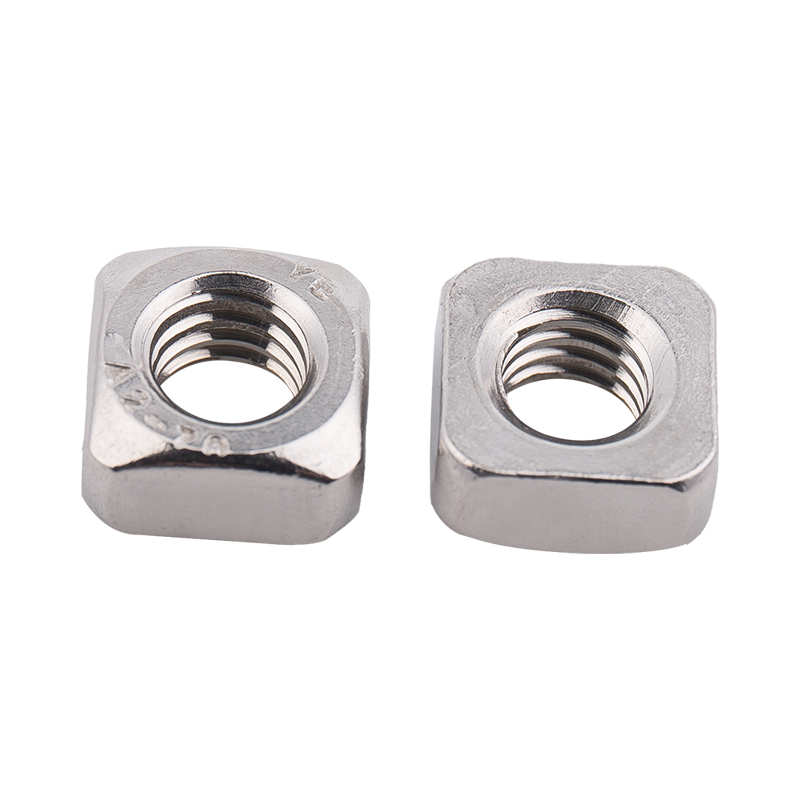
Another key advantage is the resistance of stainless steel to pitting and stress corrosion cracking (SCC), both of which are common problems in metals exposed to aggressive environments. Pitting occurs when localized areas of corrosion cause small holes or pits to form in the metal, while SCC refers to cracking caused by tensile stress in a corrosive environment. Stainless steel nuts, particularly those made from high-quality alloys, are highly resistant to these issues, further enhancing their reliability in demanding applications.
While stainless steel nuts are an excellent choice for high-stress, corrosive environments, it’s important to note that not all stainless steels are created equal. The grade of stainless steel used can significantly impact the performance of the nuts. For instance, nuts made from austenitic grades like 304 and 316 offer the best resistance to corrosion and are commonly used in the most demanding environments. However, for applications exposed to extreme temperatures or other specialized conditions, further customization of alloy composition may be required.
Overall, stainless steel nuts offer unparalleled advantages in high-stress, corrosive environments due to their corrosion resistance, mechanical strength, and durability. Their ability to perform consistently under extreme conditions ensures that they remain a critical component in various industries that require both resilience and reliability.