Thread rolling significantly improves the fatigue resistance of stainless steel bolts compared to cut threading due to several key factors related to how the threads are formed and the resulting material properties. Here’s a breakdown of how thread rolling enhances fatigue resistance:
Material Strengthening through Cold Working
Thread rolling is a cold-forming process where the threads are created by applying pressure to the bolt’s surface, causing the material to plastically deform into the desired thread shape. This cold working induces work hardening in the stainless steel, increasing the hardness and strength of the surface layer.
The cold-formed threads have higher compressive residual stresses, which means that the surface is less likely to crack under cyclic loads (repeated stresses), improving the bolt’s fatigue resistance. In contrast, cut threading removes material, leaving the threads weaker and more prone to cracking under repeated loads.
No Material Removal = Continuous Grain Structure
In thread rolling, no material is removed from the bolt. Instead, the material is displaced to form the threads. This preserves the continuous grain structure of the stainless steel, which follows the contour of the thread.
By maintaining this continuous grain flow, the rolled threads are stronger and more resistant to fatigue. Cut threading, on the other hand, severs the grain structure, creating stress concentration points that are more vulnerable to fatigue and failure over time.
Smooth Surface Finish
Rolled threads generally have a smoother surface finish compared to cut threads. The smoother surface means there are fewer surface imperfections, such as microscopic notches or tool marks, that could act as stress concentrators during cyclic loading.
In cut threads, the machining process often leaves behind small surface defects, which can initiate cracks under repeated stresses, leading to fatigue failure. Rolled threads, with their smoother surfaces, distribute stress more evenly and are therefore less likely to crack.
Residual Compressive Stress
The thread rolling process introduces compressive residual stress into the material at the thread root (the lowest part of the thread). This is beneficial because most fatigue failures begin at the surface, and the compressive stresses counteract the tensile stresses that cause cracking.
In cut threads, the machining process does not induce these beneficial compressive stresses and may even leave the material with residual tensile stresses, which promote crack initiation and propagation under fatigue loading.
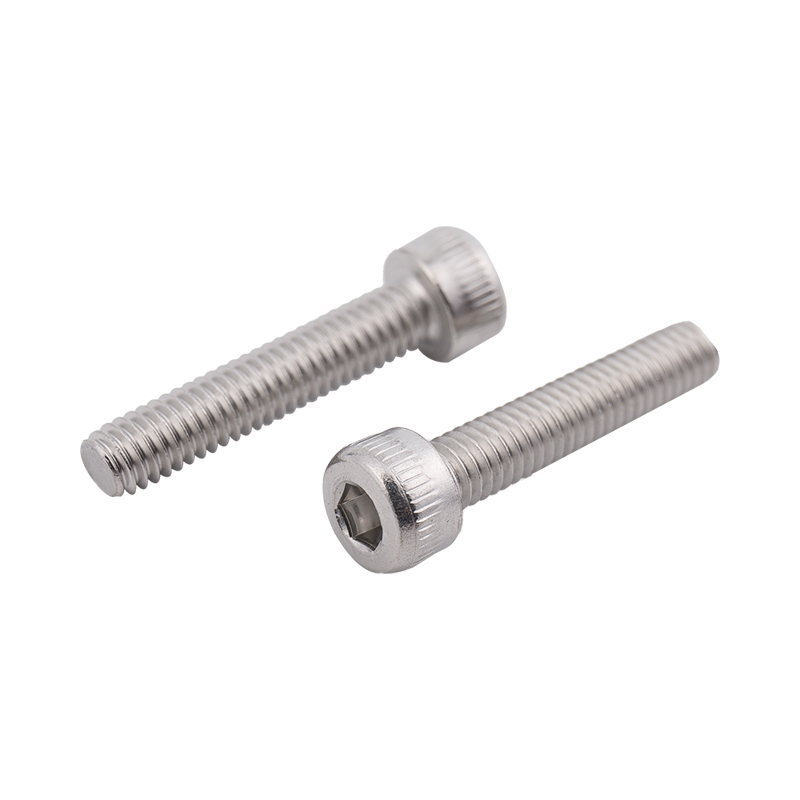
Reduced Stress Concentration
The smooth transitions and rounded contours produced by thread rolling reduce stress concentrations at critical points like the thread root. In contrast, cut threads often have sharper transitions, which act as stress risers and increase the likelihood of fatigue cracks forming in these areas.
Lower stress concentration in rolled threads means that they can endure more load cycles without failing, making them more suitable for applications where bolts are subjected to repeated loading and unloading.
Increased Fatigue Life
The combination of smoother surface finish, compressive residual stresses, continuous grain flow, and reduced stress concentrations in rolled threads greatly increases the fatigue life of stainless steel bolts. This is especially important in applications that involve dynamic or cyclic loading, such as in aerospace, automotive, and structural engineering.
Studies have shown that rolled threads can increase fatigue life by as much as four to five times compared to cut threads, making them the preferred choice for high-stress and fatigue-critical applications.
In conclusion, thread rolling improves the fatigue resistance of stainless steel bolts by:
Strengthening the material through cold working.
Preserving the continuous grain structure.
Producing a smoother surface with fewer imperfections.
Introducing beneficial compressive residual stresses.
Reducing stress concentrations at the thread root.
These factors collectively make rolled threads significantly more durable under cyclic loads compared to cut threads, improving the fatigue performance and longevity of stainless steel bolts in demanding applications.