Stainless steel screws are available in various grades, each with distinct properties suited to different applications. The most commonly used grades of stainless steel for screws are 304, 316, and 410. Here’s how their properties differ:
1. Grade 304 Stainless Steel
Composition: Contains approximately 18% chromium and 8% nickel. It is also known as A2 stainless steel.
Corrosion Resistance: Offers good resistance to corrosion, including resistance to oxidation and rust. Suitable for many indoor and some outdoor applications.
Strength: Provides good strength and is generally used for general-purpose applications.
Applications: Commonly used in environments where moderate corrosion resistance is required, such as in kitchen appliances, architectural features, and hardware.
Limitations: Less resistant to chloride-induced corrosion compared to Grade 316, so not ideal for marine environments or highly corrosive conditions.
2. Grade 316 Stainless Steel
Composition: Contains approximately 16% chromium, 10% nickel, and 2% molybdenum. It is also known as A4 stainless steel.
Corrosion Resistance: Excellent resistance to corrosion, particularly against chlorides and seawater. The addition of molybdenum enhances its resistance to pitting and crevice corrosion.
Strength: Similar to Grade 304 but with enhanced corrosion resistance. It maintains strength in more corrosive environments.
Applications: Ideal for marine environments, chemical processing, and other applications where exposure to harsh chemicals or saltwater is a concern.
Limitations: Typically more expensive than Grade 304 due to the added molybdenum.
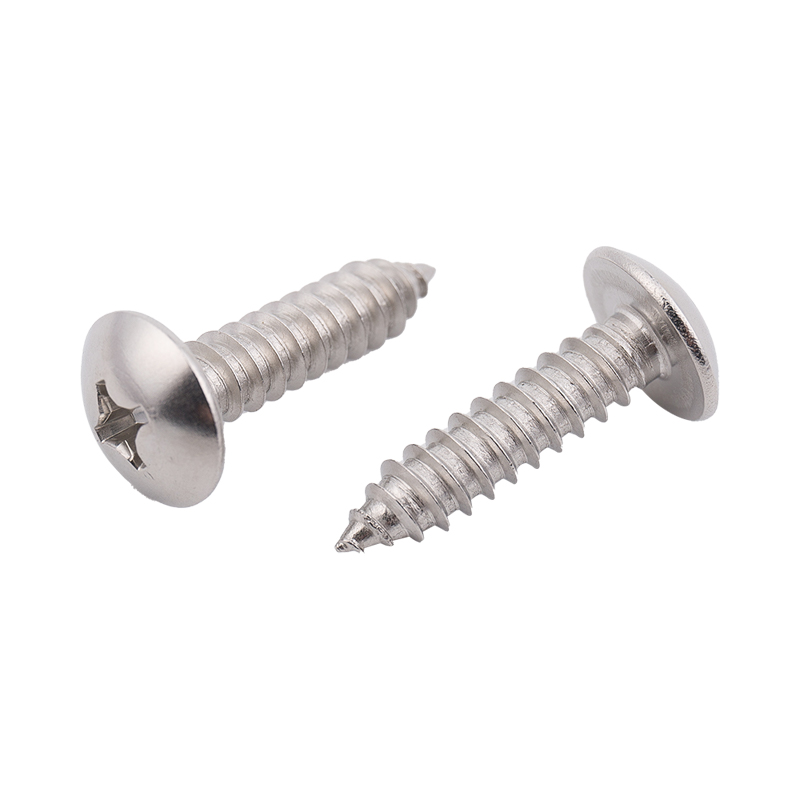
3. Grade 410 Stainless Steel
Composition: Contains approximately 11.5% chromium and minimal nickel. It is a martensitic stainless steel.
Corrosion Resistance: Provides moderate corrosion resistance. It is less resistant to corrosion compared to Grades 304 and 316, but it can be heat-treated to increase hardness.
Strength: Offers high strength and hardness, which can be enhanced through heat treatment. This makes it suitable for applications requiring wear resistance and strength.
Applications: Commonly used for making screws in applications that require high strength and wear resistance, such as in automotive and aerospace components.
Limitations: Not suitable for environments with high corrosion exposure, such as marine or chemical environments.
Grade 304 is versatile and used for general-purpose applications where moderate corrosion resistance is sufficient.
Grade 316 offers superior corrosion resistance, especially in harsh environments, and is preferred for marine or chemical applications.
Grade 410 provides high strength and wear resistance but has lower corrosion resistance compared to 304 and 316.
Choosing the appropriate grade depends on the specific environmental conditions, strength requirements, and budget considerations for the application in question.