Preventing fretting fatigue fracture of elastic retaining rings is a comprehensive engineering problem involving material selection, design optimization, manufacturing process, lubrication system, working environment control, and maintenance management. Here are some specific preventive measures:
Material selection and improvement
Evaluate material properties: Select materials with sufficient hardness, wear resistance and fatigue resistance to ensure that the elastic retaining ring is compatible with the materials of the mating surface.
Adopt advanced materials: Explore the use of advanced materials with excellent fatigue and wear resistance, such as high-performance alloy steel, stainless steel, etc.
Surface treatment technology: Use surface treatment technologies such as shot peening and nitriding to improve the surface hardness and fatigue resistance of the elastic retaining ring.
Design optimization
Optimize contact surface: Improve the finish of the mating surface and reduce friction and wear. The geometry of the contact surface should be considered during design to distribute the load more evenly and reduce stress concentration.
Adjust clearance and tolerance: Optimize the clearance and tolerance between the elastic retaining ring and the mating part to avoid fretting fatigue caused by excessive or too small clearance.
Finite element analysis: Use finite element analysis (FEA) to simulate and analyze the stress distribution of the elastic retaining ring and the mating surface, identify potential stress concentration and guide design improvements.
Manufacturing process control
Strictly control the processing accuracy: Ensure the processing accuracy of the elastic retaining ring and its mating parts to avoid stress concentration caused by manufacturing defects.
Reserve thermal expansion gap: During the design and manufacturing process, sufficient thermal expansion gap should be reserved to cope with the expansion or contraction caused by changes in the working environment temperature.
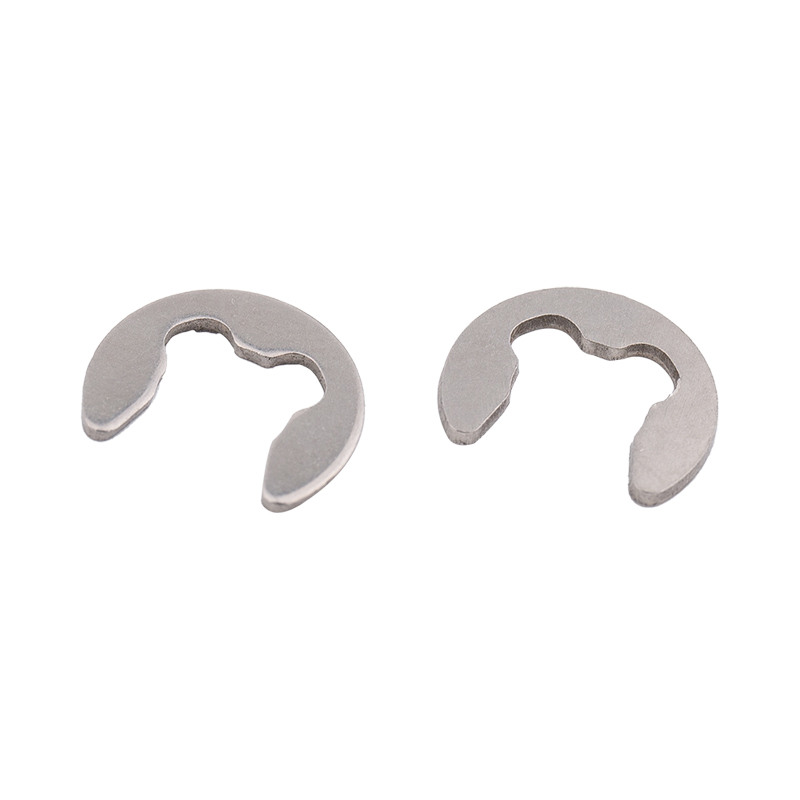
Lubrication system
Implement effective lubrication: Use suitable lubricants and establish an effective lubrication system to reduce friction and wear on the contact surface. The lubricant should be replaced regularly to ensure its stable performance.
Working environment control
Monitor and control the working temperature: Avoid excessively high working environment temperature, as overheating will accelerate micro-motion fatigue. If necessary, a cooling system should be installed to control the temperature.
Protect components from corrosion: Take anti-corrosion measures, such as using corrosion-resistant coatings or materials, to reduce the impact of corrosion on the performance of the elastic retaining ring.
Maintenance management
Regular inspection and maintenance: Develop a regular inspection and maintenance plan to detect and deal with potential problems in a timely manner. Inspections include the wear of the retaining ring, lubrication status, and tightness of mating parts.
Replacement protocol: Develop a clear protocol for replacing retaining ring parts, including when and how to replace them, to prevent premature failure.
Training and awareness: Train operators and maintenance personnel to improve their skill level and awareness, and ensure that they understand the importance of proper assembly, maintenance, and operation.
Real-time monitoring and early warning
Introduce advanced monitoring technology: Explore the use of advanced monitoring technologies such as sensors and IoT devices to continuously monitor the condition of the retaining ring and provide real-time data for predictive maintenance.
Establish a feedback loop: Establish a feedback loop with customers to collect information about actual performance and any observed problems. Use this feedback for continuous improvement.
Preventing fretting fatigue fracture of retaining rings requires a multi-faceted approach, taking into account factors such as materials, design, manufacturing process, lubrication system, working environment, and maintenance management. By implementing these measures, the risk of fretting fatigue fracture can be significantly reduced and the reliability and service life of the retaining ring can be improved.