The influence of material selection on the performance of elastic retaining rings is significant. Different materials have different physical and chemical properties, which directly affect the strength, hardness, wear resistance, corrosion resistance, elastic recovery ability and stability of elastic retaining rings in extreme environments such as high temperature and high pressure. The following is a detailed analysis of the influence of material selection on the performance of elastic retaining rings:
Strength and hardness
The strength and hardness of the material determine the ability of the elastic retaining ring to bear loads and resist deformation. High-strength and high-hardness materials can provide better structural stability and durability, and reduce deformation or fracture caused by overload or long-term stress.
Wear resistance
Wear resistance is a key factor for elastic retaining rings to maintain their shape and function during long-term use. Materials with good wear resistance can reduce the performance degradation caused by friction and wear, and extend the service life of the elastic retaining ring.
Corrosion resistance
In some application environments, elastic retaining rings may be exposed to corrosive media. Materials with good corrosion resistance can resist the erosion of these media and maintain the structural integrity and functional stability of the elastic retaining ring.
Elastic recovery ability
Elastic recovery ability refers to the ability of the elastic retaining ring to return to its original shape after being subjected to external forces. Materials with good elastic recovery ability can maintain stable performance after multiple cycles of loading, reducing failure caused by permanent deformation.
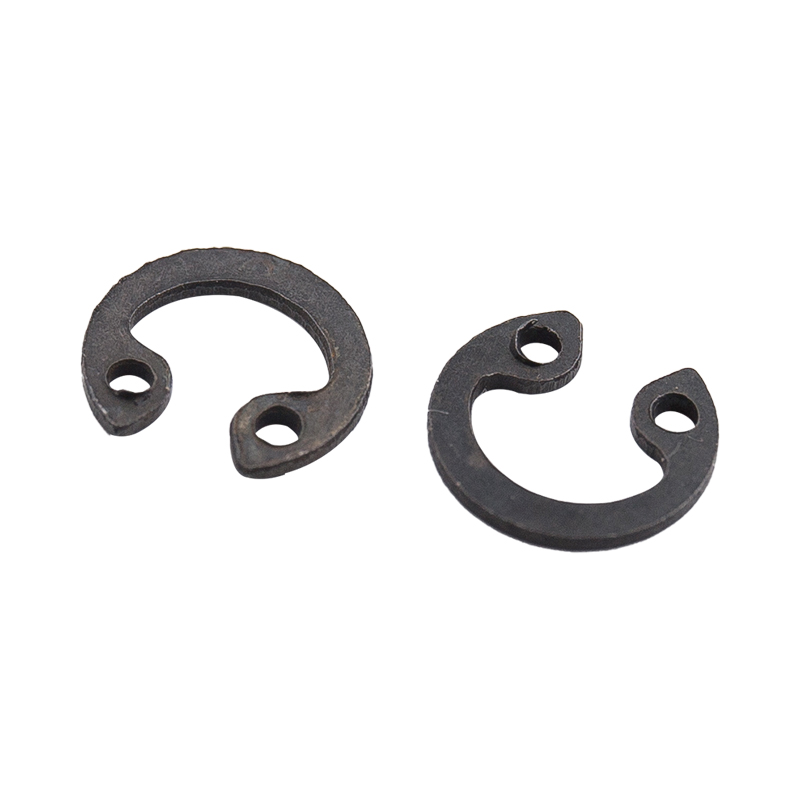
High temperature and high pressure stability
Elastic retaining rings working in high temperature or high pressure environments need to choose materials that can work stably. These materials should have good thermal stability and pressure stability to avoid softening, melting or deformation under high temperature or high pressure.
Specific material impact examples
Rubber: It has good elasticity and wear resistance and is suitable for occasions with low temperature and simpler media, such as liquid seals, gas seals, vibration elimination, etc. However, the performance of rubber materials may decrease under high temperature and highly corrosive media.
Polyurethane: It is oil-resistant, wear-resistant, and tough. It is suitable for working under harsh conditions such as high temperature, high pressure, and chemical media, such as hydraulic oil seals, automotive parts, etc.
Polyimide: A new high-performance material with extremely high strength, hardness, heat resistance and low friction coefficient. It is suitable for high temperature and high-demand environments such as aerospace, ships, and automobiles.
Fluororubber: It has the ability to work stably under extreme temperatures, chemical media and high pressures, and is suitable for aerospace, chemical, oil and gas and other industries.
Metal materials (such as stainless steel, copper, aluminum): have high durability and corrosion resistance, suitable for occasions with high strength and hardness requirements. However, the elastic recovery ability of metal materials is relatively poor and the cost is relatively high.
The influence of material selection on the performance of elastic retaining rings is multifaceted, and it is necessary to select appropriate materials according to specific application scenarios and needs. When selecting materials, factors such as strength, hardness, wear resistance, corrosion resistance, elastic recovery ability and working environment should be comprehensively considered.