Using the wrong torque value for carbon steel nuts in a structural assembly can lead to several serious consequences that affect both the performance and safety of the structure. Proper torque is essential for achieving the correct clamping force, which ensures that the components of a structure remain securely fastened and can bear the required loads without failure. Here's a breakdown of the potential consequences of using the wrong torque value:
1. Structural Failure or Weakening
Under-tightening (Insufficient Torque):
Loose Connections: If the torque applied is too low, the nut will not generate enough clamping force to securely fasten the connected components. Over time, the joint may loosen due to external forces such as vibrations, thermal expansion, or movement, potentially leading to the failure of the joint.
Risk of Shear or Slippage: In some cases, under-tightened nuts may not adequately transfer loads between the connected parts, which can lead to slippage or even shear failure of the bolt or nut. This is especially critical in high-stress applications, such as bridges or tall buildings, where joint failure can lead to catastrophic consequences.
Decreased Load-Bearing Capacity: Under-tightened fasteners may fail to distribute mechanical loads evenly across the components they are securing, resulting in uneven stress and eventual deformation or failure of the parts.
Over-tightening (Excessive Torque):
Stripped or Damaged Threads: Over-tightening a carbon steel nut can damage the threads of both the nut and the bolt, leading to stripped threads. Once the threads are damaged, it becomes difficult or impossible to achieve a secure connection, leading to the need for replacement or rework.
Deformation of Fasteners: Applying too much torque can deform the nut and bolt, potentially causing the fastener to lose its strength or functionality. This can lead to a weakened connection that may not be able to withstand the intended loads or stresses.
Material Failure: Over-tightening may lead to yielding (plastic deformation) of the material, especially in the bolt or nut. In some cases, excessive torque can even lead to the breaking of the fastener, causing an immediate failure of the joint.
2. Risk of Fatigue and Stress Concentrations
Increased Risk of Fatigue: Fasteners that are improperly torqued (either under-tightened or over-tightened) can create stress concentrations around the joint. These localized areas of high stress can cause cracks to form, which may grow over time due to repeated loading (fatigue). This is particularly problematic in structures subjected to dynamic loads, such as bridges, cranes, or machines.
Premature Failure: Incorrect torque values can reduce the fatigue resistance of the connection, leading to premature failure after repeated loading cycles. This is particularly dangerous in safety-critical applications like aircraft, where structural integrity is essential.
3. Decreased Safety Margin and Structural Integrity
Failure to Meet Design Requirements: Every structural connection is designed with a specific clamping force in mind to ensure that the materials and components can carry the intended loads without failure. Incorrect torque can mean that the fastener is not working within its designed safety margin. This reduces the overall structural integrity and may lead to failure under conditions that should have been safe.
Unpredictable Performance: Using incorrect torque values can lead to unpredictable behavior of the structure, making it difficult to anticipate how it will perform under different load conditions. This can be dangerous, as the actual performance of the assembly may differ significantly from what was expected in the design calculations.
4. Corrosion and Galvanic Issues
Increased Risk of Corrosion: Under-tightened nuts may allow moisture or corrosive elements to accumulate in the gap between the nut and the bolt, increasing the likelihood of corrosion. Corroded fasteners may degrade over time, weakening the connection and leading to failure.
Galvanic Corrosion: Over-tightening can cause mechanical damage to the coatings or surface treatments on carbon steel nuts and bolts, which can expose the metal to galvanic corrosion if different metals are in contact. The damage to protective coatings can lead to rust formation and material degradation.
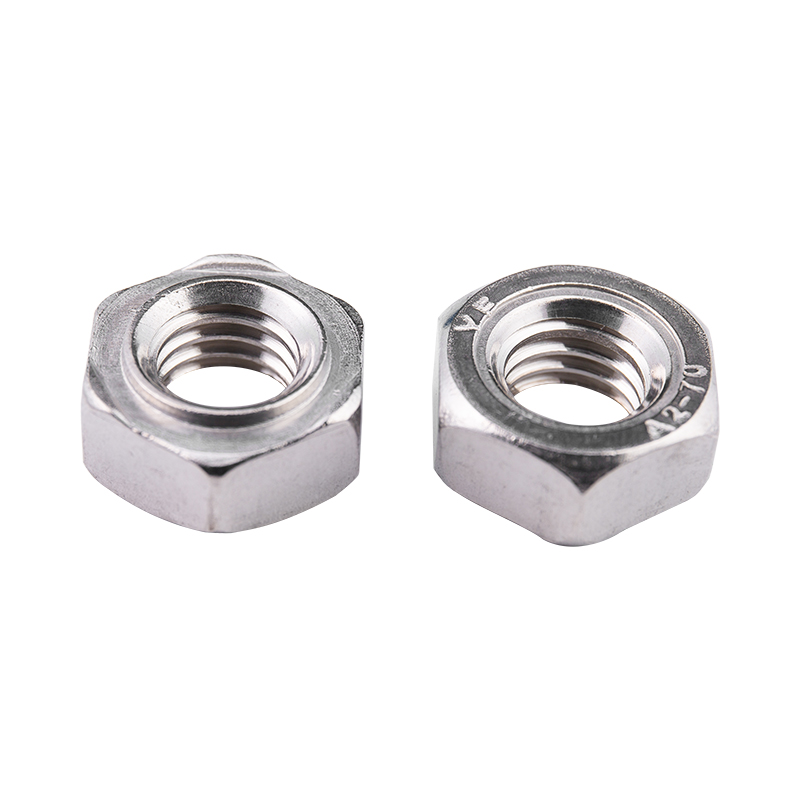
5. Potential for Nut Backing Off or Loosening
Vibration-Induced Loosening: If the torque is too low, the nut may not create enough friction to keep the threads engaged, especially in environments subject to vibration. This could lead to the nut loosening over time, causing the joint to fail. Vibration-induced loosening is a significant risk in machinery, automotive, and construction applications.
Safety Hazards: Loosening nuts in critical applications (e.g., bridges, buildings, machinery) can present serious safety hazards. A loose fastener can result in catastrophic failure, risking both structural integrity and human safety.
6. Difficult Maintenance and Repairs
Difficulty in Removal: Over-tightening may cause the threads to deform or seize, making it extremely difficult to remove the nut or bolt for future maintenance or repairs. This can lead to delays and increased maintenance costs.
Costly Replacements: Damaged fasteners resulting from incorrect torque (especially stripped threads or deformed bolts) will need to be replaced. In critical applications, this may require disassembly of large sections of the structure or machinery, resulting in downtime and additional costs.
7. Impaired Performance in Seismic or Dynamic Load Conditions
Seismic Risk: In structures located in earthquake-prone areas, the correct torque value is even more critical, as dynamic forces during an earthquake can magnify the impact of improperly torqued fasteners. If the nuts are not tightened correctly, they may fail under the stress of seismic events, leading to partial or complete collapse of parts of the structure.
Impact of Dynamic Loads: In structures or vehicles exposed to dynamic loads (e.g., machinery, vehicles, and infrastructure subjected to traffic or wind loads), incorrect torque can lead to fatigue failure or even complete failure of the assembly, endangering the entire structure.
8. Legal and Regulatory Consequences
Non-Compliance with Standards: Using the wrong torque value can result in non-compliance with building codes or industry standards (e.g., ASTM, ISO, AISC). This could lead to legal issues, fines, or even forced retrofitting or reconstruction of the structure to meet the required standards.
Liability for Failure: If a structural failure occurs due to improperly torqued fasteners, it could result in significant liability for the engineers, contractors, or manufacturers involved. This could lead to legal action, financial penalties, or reputational damage.
9. Decreased Long-Term Reliability
Inconsistent Performance Over Time: Incorrect torque can lead to unpredictable long-term performance. While a structure may initially appear stable, improper tightening can lead to delayed failures, making it difficult to detect issues until the damage becomes critical.
Reduced Service Life: The incorrect torque can shorten the service life of the entire structural assembly, as the connection may begin to degrade sooner than anticipated, necessitating early replacements or repairs.