The choice between dry film lubricants and traditional wet lubricants for carbon steel screws involves several trade-offs related to performance, application, cost, and environmental factors.
Performance
Dry Film Lubricants:
Advantages:
Provide consistent and controlled friction, leading to predictable torque-tension relationships.
Offer long-lasting lubrication that does not degrade or evaporate over time.
Resistant to washout or displacement in extreme conditions (e.g., high heat, water immersion).
Perform well in high-temperature and high-pressure environments where wet lubricants may break down.
Disadvantages:
Limited ability to reseal or redistribute lubrication after initial application.
Generally lower initial lubricity compared to wet lubricants.
Wet Lubricants:
Advantages:
Provide superior lubricity during initial installation, reducing friction significantly.
Can be reapplied easily for maintenance or reuse.
Often include corrosion inhibitors, adding extra protection.
Disadvantages:
Can degrade over time due to evaporation, contamination, or thermal breakdown.
Prone to washout in wet or humid environments, reducing long-term effectiveness.
Application and Compatibility
Dry Film Lubricants:
Advantages:
Ideal for pre-application during manufacturing, providing uniform coating.
No mess during handling or assembly, improving workplace cleanliness.
Compatible with high-speed automated assembly processes due to non-drip properties.
Disadvantages:
Requires specialized equipment for application (e.g., curing ovens).
May not adhere well to certain coatings or finishes without proper surface preparation.
Wet Lubricants:
Advantages:
Easy to apply manually or through simple machinery.
Compatible with a wide range of surfaces and coatings.
Disadvantages:
Risk of contamination in cleanroom or precision assembly environments.
Can attract dirt, dust, and debris, leading to potential thread damage.
Cost and Efficiency
Dry Film Lubricants:
Advantages:
Lower lifecycle cost due to durability and long-term performance.
Reduces the need for re-lubrication or maintenance in many applications.
Disadvantages:
Higher upfront cost for material and application processes.
Requires precise quality control during application.
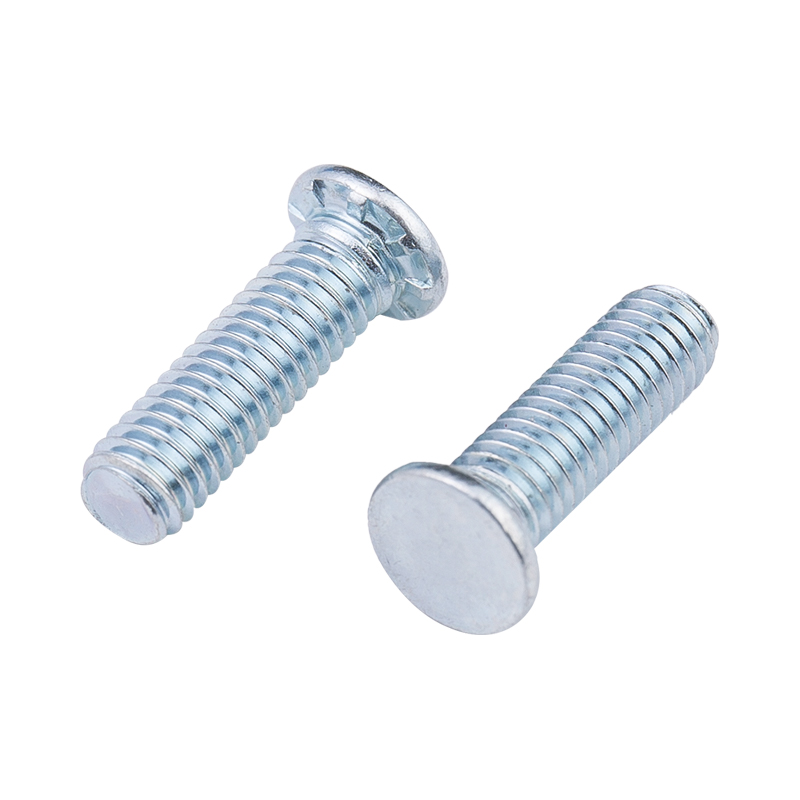
Wet Lubricants:
Advantages:
Low initial cost and readily available.
Can be applied in-field without specialized tools.
Disadvantages:
Higher maintenance costs due to frequent reapplication.
Can lead to waste and inefficiencies in certain applications.
Environmental and Safety Considerations
Dry Film Lubricants:
Advantages:
Environmentally friendly options available (e.g., non-VOC, non-toxic).
No risk of spillage, reducing environmental contamination.
Disadvantages:
Some formulations may involve hazardous chemicals during application.
Wet Lubricants:
Advantages:
Traditional products are familiar and widely used, with established safety protocols.
Disadvantages:
Risk of environmental harm due to spillage or improper disposal.
Some wet lubricants contain volatile organic compounds (VOCs) or other harmful chemicals.
Typical Applications
Dry Film Lubricants:
Aerospace, automotive, and heavy machinery where long-term performance and extreme condition resistance are critical.
Environments with high temperatures, such as exhaust systems or turbines.
Wet Lubricants:
Applications requiring frequent adjustments or reassembly, such as maintenance-heavy equipment.
Scenarios with low exposure to extreme conditions, such as indoor machinery or short-term installations.