The trade-off between increased tensile strength and reduced ductility in carbon steel screws is a crucial factor when selecting screws for specific applications. Here's a breakdown of how these two properties interact and the impact of their balance on performance:
1. Tensile Strength vs. Ductility:
Tensile Strength refers to the maximum stress a material can withstand while being stretched or pulled before breaking. Higher tensile strength makes a screw more capable of bearing heavy loads and resisting deformation under stress.
Ductility is the ability of a material to deform under tensile stress without breaking. Materials with high ductility can absorb energy and undergo significant plastic deformation before failure, which is critical for preventing sudden, brittle fractures.
2. Impact of Increased Tensile Strength:
Higher Load-Bearing Capacity: Increased tensile strength enables carbon steel screws to withstand higher loads and stresses without failing. This is particularly important in heavy-duty applications where screws must bear substantial mechanical forces, such as in construction, automotive, or industrial machinery.
Increased Brittle Behavior: However, as tensile strength increases (especially in high-carbon steels), the material becomes less able to absorb stress through plastic deformation. This leads to reduced ductility, making the screw more prone to brittle fracture under sudden or shock loading conditions, which can be catastrophic in some applications.
Fatigue Resistance: While higher tensile strength can improve resistance to static loads, it can sometimes reduce fatigue resistance in cyclic loading environments. This is because the material may not flex or deform as much, causing it to fail after repeated stress cycles.
3. Impact of Increased Ductility:
Improved Resistance to Fracture: Higher ductility means the screw can deform plastically without breaking, which is beneficial when the screw is subjected to dynamic loading, vibration, or shock forces. Ductile materials tend to "bend" rather than snap, making them more forgiving in applications that involve fluctuating or unpredictable stresses.
Lower Load-Bearing Capacity: While ductility helps prevent sudden fracture, it comes at the expense of lower tensile strength. Ductile screws are more likely to experience permanent deformation (e.g., bending or elongation) under high loads, reducing their effectiveness in high-stress applications. This makes them unsuitable for high-torque or heavy-load environments where screw integrity needs to be maintained.
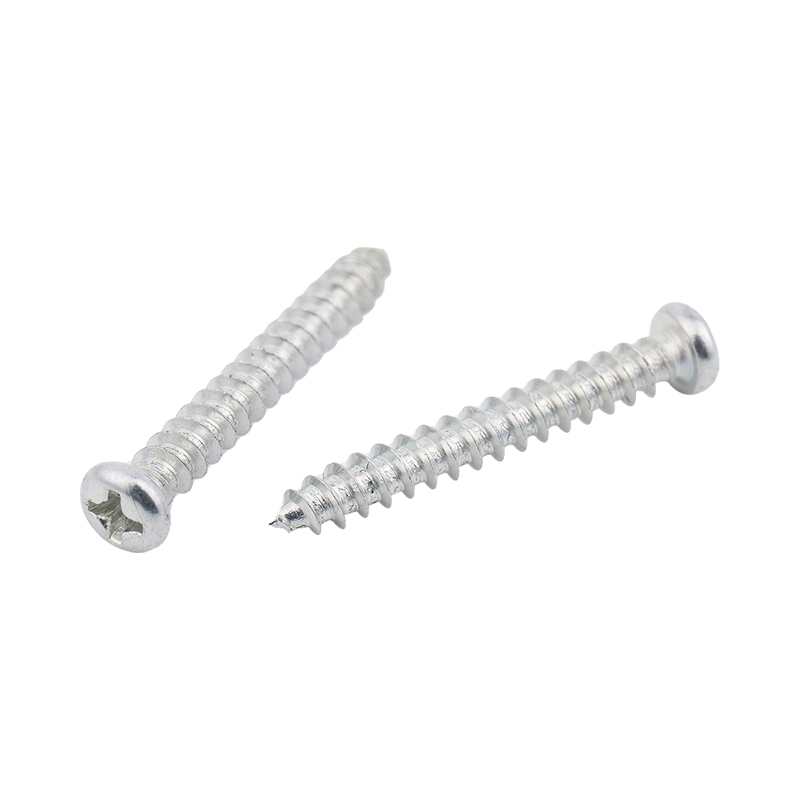
4. Practical Considerations:
Application-Specific Requirements: The choice between higher tensile strength and ductility depends largely on the application. For example, in construction or aerospace, where high load-bearing capacity and strength are paramount, screws with higher tensile strength (low ductility) are preferred. Conversely, in applications where vibration resistance, shock loading, or safety (e.g., in automotive or machinery maintenance) is important, screws with higher ductility and lower tensile strength are used to prevent catastrophic failure.
Temperature Sensitivity: In extreme environments, such as high temperatures or cryogenic conditions, the balance between tensile strength and ductility becomes even more critical. At higher temperatures, materials with high tensile strength may lose their resistance to deformation, reducing their ductility and potentially leading to failure. Conversely, materials with better ductility can handle thermal expansion and contraction more effectively.
5. Processing Trade-offs:
Heat Treatment: The heat treatment process plays a significant role in controlling both tensile strength and ductility. For example:
Quenching and tempering can increase tensile strength while maintaining a balance of ductility.
Carburizing may increase surface hardness, making the screw more resistant to wear but at the expense of ductility.
Cold Heading vs. Hot Forging: Cold-heading processes typically lead to higher tensile strength but may reduce ductility, while hot-forging can allow for greater ductility but might result in a lower tensile strength.
6. Overall Trade-Off Summary:
Higher tensile strength = greater load-bearing capability but reduced ability to absorb shock or deformation (brittle fracture risk).
Higher ductility = better shock resistance, more flexibility under stress, but lower load-bearing capacity and potential for deformation under heavy loads.